Inline full inspection of optical irregularities
Identification of defect location and prevention of leakage
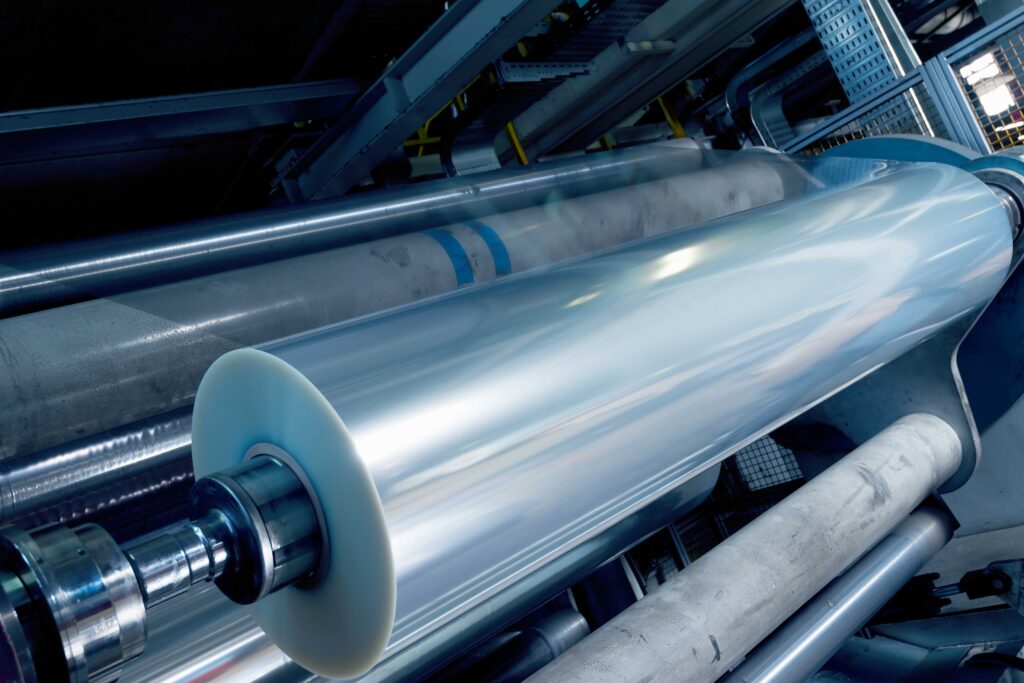
While not having been a concern in the past, retardation films for LCDs are increasingly drawing attention to optical irregularities, along with the growing need for higher resolution and higher image quality in smartphone screens. In particular, unevenness in the form of streaks or spots reduces the contrast of the display and is easily perceived as a defect by the human eye on the final LCD product. Against this background, quality requirements for retardation and orientation of retardation film and linear polarizing film are increasing.
However, with conventional point measurement systems, there are uninspected areas due to inspection at fixed positions or in traverse scanning paths, so optical irregularities that occur in these areas are not detected and reduce the overall yield and quality of the product.
With KAMAKIRI, the entire film surface is inspected. Therefore, even if a sudden optical irregularity occurs, an alarm can be generated real-time, to prevent any defective area outflow. In addition, since the entire surface data is saved at the manufacturing stage, KAMAKIRI is also effective in analyzing the cause of any problems that may occur later while using the film.
Since its launch in 2014, KAMAKIRI has been introduced to optical film manufacturers for displays in numerous locations, including Japan, Korea, China, and Taiwan.
Optimization of process in short time
In the field of process development, there is always a need to quickly find the optimal conditions. In addition, when many types of films are produced on a single line, the process needs to be checked each time the line is switched to a different product. In such cases, KAMAKIRI’s ability to check changes in optical characteristics in real time while fine-tuning various production conditions strongly supports overwhelming efficiency improvements.
Stabilization of the production system, which has until now relied on craftsmanship, becomes a reliable and efficient process based on data acquired with KAMAKIRI.
Spot unevenness MD thread
Inline Evaluation of Film Temperature
In film production, temperature control is a major factor in determining film characteristics.
It has been difficult to measure in-plane temperature irregularities in transparent film, but combining the KAMAKIRI system with an infrared camera now makes it possible to evaluate temperature irregularities at the die exit, to detect temperature changes in the contact area with chiller rolls, and to evaluate temperature irregularities in the heater section.
General Thermography Our product A67 series
Evaluate background temperature Evaluate surface temperature
Category
- #Full-length, full-width film quality control solutions
- #In-line/off-line mapping-type birefringence measurement system
- #Birefringence Measurement System
- #birefringence
- #Film