R&D and applications for next-generation laser processing
Beam shape control, polarized beam control, heat distribution imaging, laser source improvement, etc.
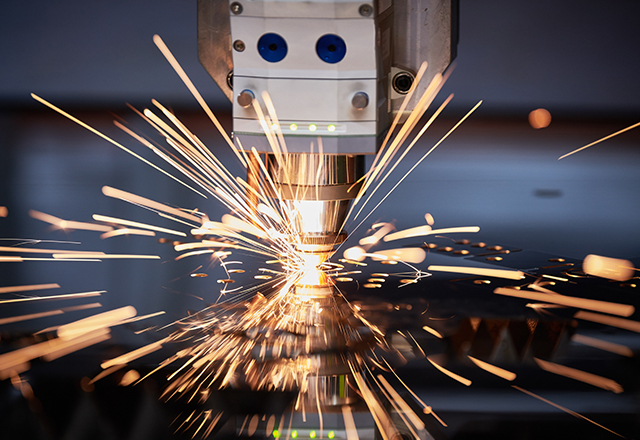
Laser processing technology continues to make remarkable progress, and is expanding into new markets such as automobiles, fuel cells, etc. In the future, this technology will be used for processing crystalline and bio-materials. The number of applications for laser processing are diverse, including cutting, welding, drilling, grooving, and surface modification. Recently, the output power and processing speed of lasers have become higher. The enhanced performance enables users to design ideal laser processing methods based on their unique application requirements.
This breakthrough in laser processing technology is largely due to the rise of fiber laser technology. Fiber lasers consume less power, can be handled more flexibly, have shorter wavelengths, and higher absorption rates than conventional CO2 lasers. These characteristics enable fiber lasers to process materials at higher speeds than CO2 lasers.
In addition to faster processing speeds, fiber lasers offer a diverse set of new applications in fields such as cutting, hole drilling, groove formation, and welding. Each of these applications come with their own set of issues such as the need to improve cutting surface quality and spatter reduction in welding. To address these needs, research and development is growing to improve processing accuracy, maintain beam quality and to control wavefronts on irradiated surfaces. Furthermore, fiber laser processing has a number of potentially fatal challenges that need to be addressed; namely dirt on cutting surfaces, change in cutting sharpness, tapered surfaces and change in cross sections after cutting.
There are high expectations to use “polarization control technology” as a means to improve both laser processing speed and beam quality. It is well-known that the local absorption can be controlled by adjusting the laser polarization axis. Polarization control allows improvement tothe shape of the processed area and improves the cutting speed.
The benefits of polarization control technology extend beyond better processing speed and beam quality. Using the wavefront control prinicple of the Pancharatnam-Berry phase, a device with spatial patterning of different polarization axes can be used to achieve highly precise beam shaping. For example, in the field of spatterless welding, the beam shape (central beam + ring beam) is controlled to prevent fire onto and roughness of the work surface due to spatter.
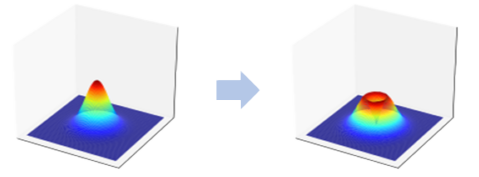
Beam shaping using photonic crystals.
e.g. Gaussian distribution into doughnut shape.
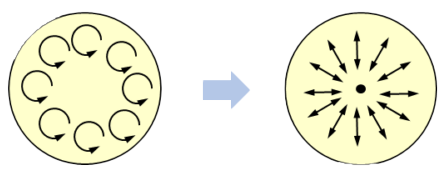
Polarization distribution control using photonic crystals
e.g. Converting uniform circularly polarized light to radially linearly polarized light distibution.
While technologies such as DOE, aspheric lenses (such as axicon), spatial light modulators, homogenizers, and field mapping have been proposed as conventional beam control methods, their use is often limited in terms of beam shape accuracy, wavelength bandwidth, and light propagation speed. There are also issues related to prototyping in that flexible and speedy prototyping cycles are needed to match specific processing applications are difficult to achieve. In addition, to use such technologies to improve beam quality, it is necessary not only to develop control methods for beam shape, wavefront control, and polarization components, but also to construct an optimum optical system to confirm the the desired processing effect.
Photonic Lattice offers its unique polarization beam shaping technology, which enables us to provide a variety of high-precision beam control elements. Furthermore, Photonic Lattice has created a vertically integrated in-house production from fundamental element design to manufacturing. Using our know-how we provid prototype and mass production services to quickly respond to the diversifying needs of the laser processing industry.
In addition, to evaluate laser processing performance, we have technologies for visualization using a high-speed camera, thermal distribution using an infrared camera, and evaluation of internal strain using a polarization camera. We will contribute to higher precision in laser processing by providing not only optical elements but also integrated solutions including precise evaluation.

Temperature distribution of work piece in laser welding.
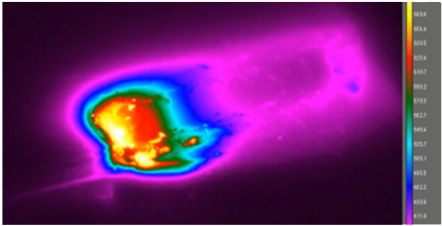
High-speed thermal imaging of welding pools
High-speed camera imaging of CO2 laser welding.
Category
- #Ultra-precision micro laser processing solutions
- #Photonic Crystal Polarizing Optical Components